Collect, Convert, or Combust? An Effective Approach to Pneumatic Waste Gas Venting
- Clear Rush Co.
- Mar 29, 2021
- 2 min read
Updated: Jun 6, 2023
Methane, the primary component of natural gas, has a greenhouse gas intensity 25 times greater than carbon dioxide. The oil and gas sector is responsible for 44% and 31% of all methane vented each year in Canada and the United States, respectively. In both the United States and Canada, over a third of this sector’s methane venting is due to gas-driven pneumatic controllers and pumps.
Pneumatic device operation
In gas-driven pneumatic systems, the pressure of the natural gas provides the motive force to shift a valve or stroke a pump and is then discharged to the atmosphere. These well-site instruments are popular around the world because of their low capital and operating costs by leveraging the gas production on site.
Regulations are changing in Canada
New regulations have been introduced in Alberta and British Columbia to phase out gas-driven pneumatics. In Saskatchewan, there are no specific requirements, however, producers are facing methane reduction targets with costly penalties for non-conformance. See the table below for a summary of the regulations across Canada.

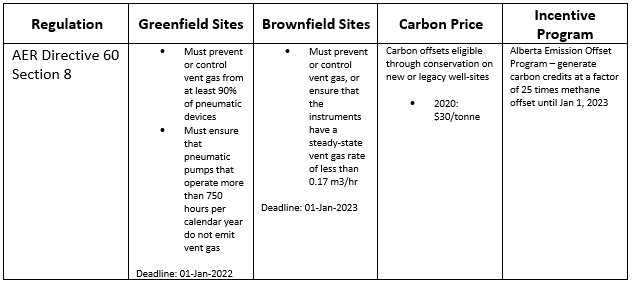
What solutions are available?
Production companies that own the underground reservoir produce and manage the fluids differently depending on the installed surface facilities. Some may supply their well-sites with natural gas by pipeline from compressor stations or plants while others recycle the produced gas from the wells on-site.
Regardless of supplied or recycled gas usage, pneumatic devices such as valve and level controllers or chemical injection pumps are generally used to manage the fluids. In these cases, the instruments vent gas to the atmosphere resulting in greenhouse gas emissions.
Three common solutions are available to solve this issue:
Electrification – conversion of gas-driven instruments to electric ones
Instrument Air Conversion – utilize compressed air to drive instruments
Combustion – collect vent gas into an enclosed vapour combustor
Electrification technology is expensive and often not economical. In many cases, in addition to purchasing pricey new instruments, the operator will need to install electrical service to the site if none already exist. For many remote locations, the costs of this method are prohibitive.
Instrument air technology is a proven method for remote well-sites and larger facilities. The disadvantage of turn-key instrument air packages is the associated costs, including expensive implementation, lengthy lead times and significant ongoing maintenance requirements. Even short and small maintenance tasks can result in significant production downtime for an entire site.
Is there a better option?
A novel, cost-effective solution that reduces emissions and complies with regulations is to collect and combust the waste gas emitted by pneumatic devices through an enclosed vapour combustor.
Exhaust from gas driven pumps and controllers is collected into a main header that is further collected into a low-pressure combustor.
Clear Rush Co. combustors are equipped with high efficiency burners that provide continuous burning capabilities, high destruction efficiencies, low emissions, zero odours, no visible flame, and increased flame stability with wide turndown ratios. Furthermore, Clear Rush Co. enclosed vapour combustors are the most reliable and cost competitive option available on the market for both new construction and retrofits.
Ensure compliance using proven, economical solutions.
Clear Rush Co. has a proven track record of helping operators overcome challenging regulatory requirements with a variety of tailor-made solutions. With our design experience and knowledge of industry requirements, we can help your organization meet its emission reduction goals. Contact us today to find out how we can help.
Connect with us to learn more: www.clearrushco.com
Comments